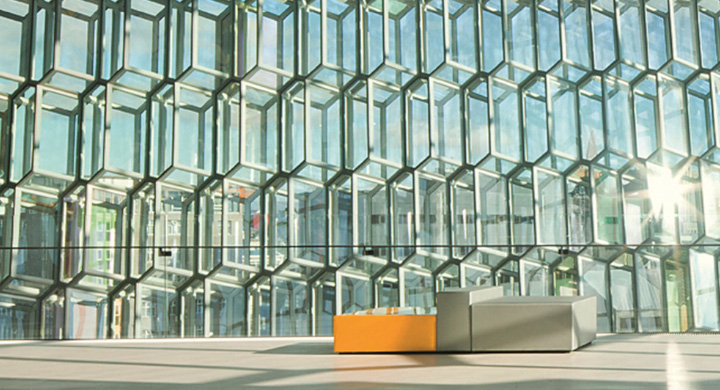
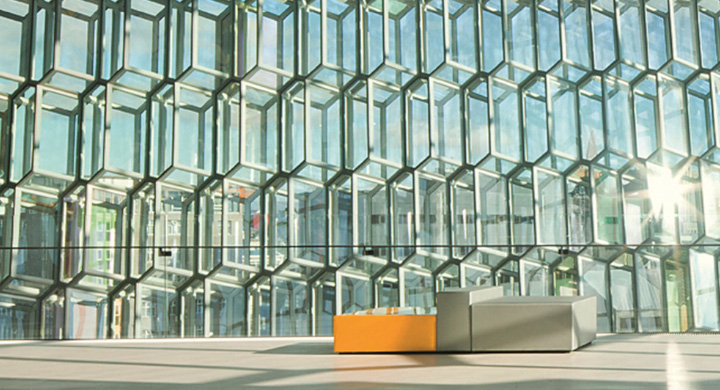
Autonomous driving
LiDAR and radar components and materials
Communication systems
Touchscreens and displays
Design and glazing
Interior and exterior glazing
E-mobility
Components and specialty glass for electronic mobility
Lighting
Exterior and interior lighting
Safety and foresight
For improved automotive safety
Sensors and electronics
Protecting and powering automotive electronics
Cosmetics
Bioactive glass for cosmetics and cosmeceutical products
Dental
Specialty glass materials and components for dentistry
Implants
Customized packaging for implantable devices
Laboratory and diagnostics
Innovative solutions for laboratory and diagnostic uses
Medical devices
Components for illumination and protection of electronics
Pharma
Pharma packaging, tubing and components for the pharma industry
Components for industrial plants
Glass materials and components for manufacturing uses
Electronics and microscopy
Electrical feedthroughs and lighting components for industrial applications
Energy generation and transportation
Components and materials for increased safety and efficiency
Energy storage
Products for durable and safe batteries and capacitors
Green tech
Innovative products supporting sustainability and renewable energy
Safety and inspection
Sprinkler systems, spark and flame detection, and head-mounted displays
Biophotonics
Advanced optics for biophotonics and medicine
Consumer optics
Cut-off filters, lenses, and blue filter glass
Laser optics
Laser optics for metrology, medicine, and rangefinders
Machine vision
Glass components and lighting for machine vision
Optical metrology
Broad spectrum of optical solutions
Sport optics
High-quality optics and technology
Protection
Protective glass for security and defense
Safety and security
Solutions for cameras, security screening, and batteries
Sensors and electronics
Reliable components for surveillance, power supply, communication, and monitoring systems
Situational awareness and sighting
Imaging technologies and materials
Data and telecommunication
Hermetic packages and glass materials for optoelectronics, antennas, and IC packaging
Electronic integration
Innovative solutions for compact, lightweight, and miniaturized devices
High performance computing
Specialty materials and components for high performance and long-term functionality
Lithography
Display and IC lithography glass technology
MEMS
Highly robust, precise, and miniaturized packaging components and materials
Wafers
Innovative wafer glass, WLCSP, and passivation products
Pharma Analytics
From chemical durability and E&L to system performance and mechanical stability
Technical Glass Tubing Consulting
Processing of glass tubing and application engineering
Pharma Consulting
Consulting for pharma glass tubing and pharma packaging
Nuclear Equipment Testing
Testing and qualification of nuclear electrical components and systems
Diagnostic and life science services
Design, development, and manufacturing of IVD consumables
Spirit
Understand more about the unique SCHOTT Spirit
Benefits
Discover the range of benefits enjoyed by SCHOTT employees
Diversity and Inclusion
Find out how our Best Teams program creates an environment for ideas and innovation
SCHOTT around the world
Discover the worldwide employer SCHOTT
Experiences
Learn more about working at SCHOTT through our employees
Our Purpose
We pioneer the impossible to make life richer while changing the world for the better
Annual Report
Key numbers and statistics from the global SCHOTT organization
Management
Information on the SCHOTT Management Board and Supervisory Board
History
Over 140 years of exciting corporate and innovation history
Carl Zeiss Foundation
The unique corporate model of SCHOTT
Research and Development
One of the world’s leading centers for glass innovation
Regions and Locations
Details of all SCHOTT production sites around the world